We use cookies on this website to improve safety and your experience. Read more.
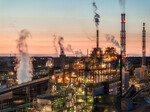
Technology
We use two technologies to produce shale fuel oil: Petroter and Kiviter. VKG’s production territory at Kohtla-Järve features three Petroter shale oil plants: Petroter I (2009), Petroter II (2014) and Petroter III (2015), along with two Kiviter shale oil plants.
The average annual processing capacity of the five production units is about five million tons of oil shale, 70% of which is provided by the Petroter plants.
How does the Petroter technology work?
Developed and patented by VKG’s own engineers, the Petroter oil shale processing technology has been used by the group since 2009. A decade of use has proven its robustness and efficiency. In 2018, for example, the three Petroter plants were active for a total of 905 days and their average net efficiency indicator was 90.5%.
The Petroter technology is based on a thermal processing (pyrolysis) process, using a mixture of fine-grained oil shale (0–25 mm fraction) and a solid heat carrier, i.e. ash. Oil shale and hot ash are mixed in a rotating reactor in the absence of air, the mixture is heated and, at around 450–500 °C, the organic matter in oil shale begins to separate out as liquids and gases. The vapour-gas mixture thus obtained is refined from ash and mechanical impurities and distilled into liquid products and gas with a high heating value.
The liquid products are forwarded to the loading department as finished products or for further processing. The gases are transmitted to the thermal power station for heat and power production. The steam is used for power production at the thermal power station. The by-products of this process include phenol water, flue gases and ash from thermal processing.
How does the Kiviter technology work?
The group currently operates two shale fuel oil plants based on Kiviter technology: Gas Generation Plant No 4 (1943) and Gas Generation Plant No 5 (1951). A 1000-ton gas generation plant (1981) has been shut down since March 2020 due to a shortage of raw materials.
The production is based on the process of pyrolysis. The heat required for pyrolysis is obtained by burning a part of the gas formed during pyrolysis. The process takes place in a vertical retort with a cross-sectional heat carrier. The Kiviter technology for oil shale thermal processing uses a 25–125 mm fraction of oil shale, which is fed into the retort from above. The oil shale moves from the loading box through a pyrolysis chamber, and mixes with a perpendicular flow of flue gases produced by burning the producer gas.
The oil and water vapours and gas produced in the course of pyrolysis exit the top of the generator into a condensation unit, where they condense into oil and water. The crude shale oil is conveyed into the preparation and then distillation units, and the wastewater into the phenol recovery unit. The producer gas is partially used to produce the heat necessary for the process and partially directed to a thermal power plant for heat and power production. The semi-coke produced in the pyrolysis process is discharged through the retort base and stored in a semi-coke storage facility.
A by-product of the Kiviter technology is phenolic water, from which we refine valuable high-purity (up to 99.8%) chemicals.
The world’s longest oil shale value chain
Our century-long experience in refining Estonian oil shale, along with the know-how we have developed in maximising the amount of oil and valuable by-products, is unique worldwide. Our oil shale plants are robust and efficient, as evidenced by our production statistics and minimal maintenance downtime.
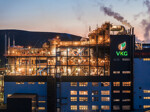
Reliable and efficient technology
Viru Keemia Grupp has undoubtedly the best results in ex-situ oil shale processing projects for shale oil generation. For us, the success indicator for research, engineering and construction projects is the time taken from the beginning of the capital-intensive construction stages to the achievement of stable total effective equipment performance. With the development of Petroter technology, we have reached the stage where the time from the launching of the initiation stage to working at full capacity is just two weeks.
We have been producing shale oil from oil shale since 1924. We have been processing oil shale with Kiviter technology for over 80 years and we have been developing Petroter technology since 2005. Today, the group has three Petroter oil shale plants and three Kiviter factories working at full capacity.
Petroter shale oil plants are characterised by reliability and energy efficiency. In 2018, the three Petroter plants operated for a total of 905 days and the average net efficiency of oil shale processing was 90.5%.
2002We conducted research with fine-grained kukersite oil shale. |
2002 – 2005We conducted an initial economic and capacity assessment feasibility study. |
2005Pre-project planning began. |
Petroter I
Project launch, zoning plan development
Construction work
The plant reaches 65% of monthly oil shale processing capacity; full capacity reached in summer 2010
Inauguration celebrations
Large-scale reconstruction
Petroter II
Project launch, zoning plan development
Construction work
Start up
Full capacity reached in early September; nominal capacity achieved within the month
Inauguration celebrations
Petroter III
Project launch, zoning plan development
Construction work
Set-up and start up
The plant reached nominal capacity within one week
Inauguration celebrations